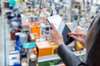
Welcome to the Senseye Predictive Maintenance resources hub
Helping you look beyond single assets and production lines, Senseye Predictive Maintenance offers a range of solutions that can fundamentally redefine maintenance processes throughout your organization. Use our comprehensive collection of resources to keep up to date with the latest industry best practices and updates.